Eigenschaftsgeregelte Prozessgestaltung des Freiformbiegens unter Berücksichtigung der Halbzeugeigenschaften
Die zentrale, innovative Idee des Vorhabens liegt in der Entwicklung eines anforderungsgerechten modellbasierten Regelungssystems, das aus prozessparallel einsetzbaren Softsensoren sowie physikalischen oder empirischen Modellen besteht. Dieses System kann indirekt und direkt eine Überwachung vor und nach dem Umformprozess sowie die Regelung schwer erfassbarer mechanischer Werkstoffeigenschaften ermöglichen.
Innovativ ist dabei insbesondere die modellbasierte Inline-Überwachung von mechanischen Werkstoffeigenschafen mit hoher Orts- und Zeitauflösung auf Basis der kombinierten Erfassung verschiedener mechanischer Zustandsgrößen des Freiformbiegeprozesses. Die indirekte Überwachung erfolgt über Sensoren zur Kraftmessung am Werkzeug, um modellbasiert Rückschlüsse auf die mechanische Bauteilbelastung zu ermöglichen.
Daraus werden mit Hilfe empirischer, physikalischer und numerischer Modelle die resultierenden Werkstoffmodifikationen bestimmt. Der parallele Einsatz eines mikromagnetischen Wirbelstrommessverfahrens ermöglicht eine direkte Messung der magnetischen Kenngrößen, wie z.B. das magnetische Barkhausenrauschen, Überlagerungspermeabilität und Wirbelstromimpedanz, durch die mit Hilfe von Korrelationen auf die mechanischen Eigenschaften vor und nach der Umformung rückgeschlossen werden kann.
Zusätzlich zu den Einzelentwicklungen liegt die Innovation des beantragten Forschungsvorhabens in der Integration in ein robustes Überwachungs- und Regelungssystem sowie die gezielte Erweiterung der regelbaren Freiheitsgrade der Freiformbiegeanlage im FBM-Verfahren.
Ergebnisse der 1. und 2. Projektphase
In Förderperiode 1 wurde die grundsätzliche Regelbarkeit der mechanischen Eigenschaften beim Freiformbiegen basierend auf einem Softsensor aufgezeigt. Dazu wurde das nicht-tangentiale Biegen im Freiformbiegeprozess als neuartige Biegestrategie implementiert, die es durch eine Spannungsüberlagerung erlaubt, die Geometrie von den mechanischen Eigenschaften zu entkoppeln. Um die nicht direkt messbaren mechanischen Eigenschaften während des Biegens herzuleiten, wurde ein Softsensor etabliert, der basierend auf Härtemesswerten die lokalen Festigkeiten, die Duktilität und die Umfangseigenspannungen herleitet. Außerdem wurde ein phänomenologisches Modell erstellt, welches die Basis für die Ursache-Wirkungs-Analyse zwischen mechanischen Eigenschaften und Biegeparametern des Prozesses in einer Regelstruktur vereint. In Förderperiode 2 lag der Fokus auf der Weiterentwicklung der Softsensorik unter Berücksichtigung der Störgrößen. Neben dem Freiheitsgrad der Anlangenkinematik wurde der Freiheitsgrad der Temperatur erforscht. Es lassen sich Unterschiede in den mechanischen Eigenschaften messen, allerdings ist die Stellgröße Temperatur schwerer regelbar als die Anlagenkinematik, weshalb das nicht-tangentiale Biegen zur Entkopplung von Geometrie und Eigenschaften im Fokus liegt. Basierend darauf wurde die Softsensorik weiterentwickelt. Sie ermöglicht auf BHN-Messungen beruhend den Axialeigenspannungszustand im nicht-tangential gebogenen Rohr mit hoher Genauigkeit unter Beachtung des Messrauschens vorherzusagen. Weiterhin folgt die Implementierung des Prozessrauschens im Softsensor. Aufbauend darauf wurde das phänomenologische Modell um das nicht-tangentiale Biegen und dessen Einfluss auf die Eigenspannungen und Geometrie erweitert sowie unter Optimierung der Reststrategie beider Parameter etabliert.
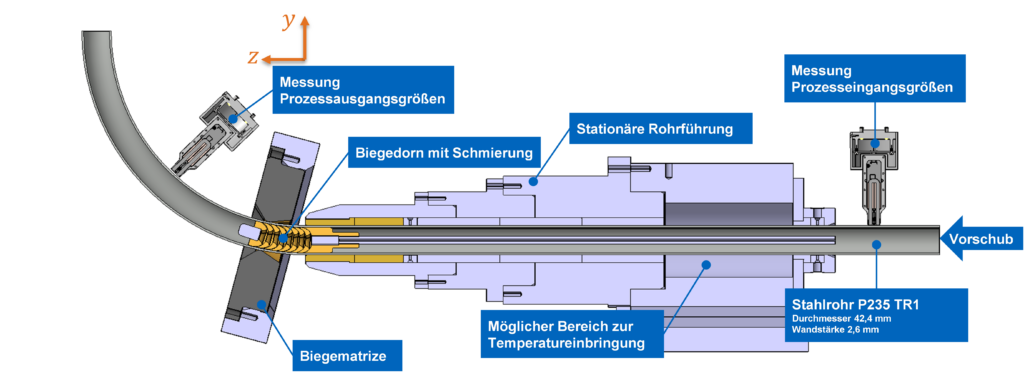
Ziele der 3. Projektphase
Die wesentliche Herausforderung der Förderperiode 3 ist die Umsetzung einer echtzeitfähigen Eigenschaftsregelung an der Versuchsanlage und der quantitative Nachweis des positiven Effekts der Eigenschaftsregelung anhand von gebogenen Bauteilen. Auf Grundlage der bereits erzielten Erkenntnisse aus Förderperiode 1 und 2 können die geplanten Teilziele für das Erreichen der echtzeitfähigen Eigenschaftsregelung für das Freiformbiegen folgendermaßen formuliert werden:
1. Umsetzung des eigenschaftsgeregelten Freiformbiegeprozesses mit bewegter Matrize in Echtzeit mit kontinuierlichem Vorschub unter produktionsnahen Bedingungen
2. Nachweis des positiven Effekts der Eigenschaftsregelung bei freiformgebogenen Bauteilen anhand von Versuchen
3. Nachweis der Übertragbarkeit der Eigenschaftsregelung auf einen höherfesten Stahl bzw. einen ferritischen Edelstahl sowie komplexere Bauteilgeometrien 4. Ableitung von Gestaltungsprinzipien für den eigenschaftsgeregelten Freiformbiegeprozess
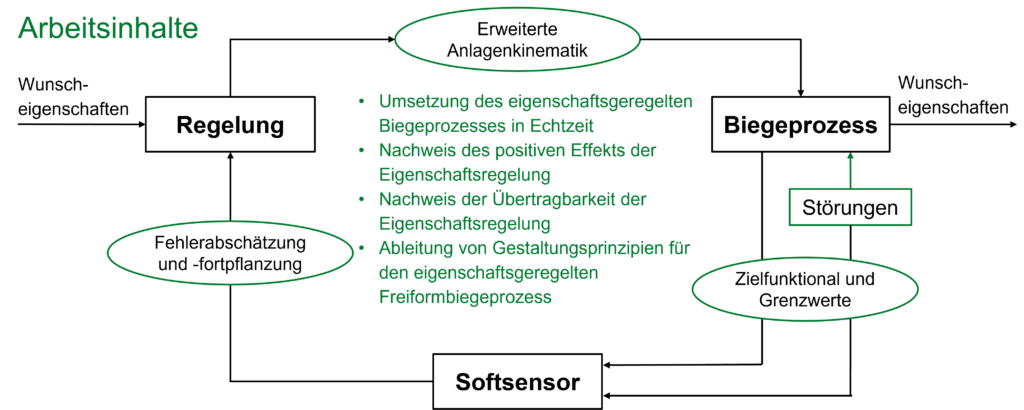
Kontakt
Lehrstuhl für Regelungstechnik der Technischen Universität München
Projektleiter: Prof. Dr.-Ing. Boris Lohmann
Projektbearbeiter: Ahmed Ismail, M.Sc. / a.ismail@tum.de
Lehrstuhl für Werkstoffmodellierung in der Umformtechnik der RWTH Aachen
Projektleiter: Prof. Dr.-Ing. Sebastian Münstermann
Projektbearbeiter: Linghao Kong, M.Sc., linghao.kong@ibf.rwth-aachen.de
Lehrstuhl für Umformtechnik und Gießereiwesen der Technischen Universität München
Projektleiter: Prof. Dr.-Ing. Wolfram Volk
Projektbearbeiter: Viktor Böhm, M.Sc. / viktor.boehm@tum.de
Veröffentlichungen
- D. Maier, S. Stebner, A. Ismail, M. Dölz, B. Lohmann, S. Münstermann, W. Volk, “The influence of freeform bending process parameters on residual stresses for steel tubes,” AIME, 2, 2021, doi: 10.1016/j.aime.2021.100047.
- D. Maier, C. Kerpen, M. Werner, L. Scandola, P. Lechner, S. Stebner, A. Ismail, B. Lohmann, S. Münstermann, W. Volk, “Development of a partial heating system for freeform bending with movable die,” in Proceedings Hot Sheet Metal Forming of High-Performance Steel.
- S. Stebner, S. Balyan, D. Maier, A. Ismail, M. Dölz, B. Lohmann, W. Volk, S. Münstermann, “A System Identification and Implementation of a Soft Sensor for Freeform Bending,” Materials, 14(16), 2021, doi: 10.3390/ma14164549.
- S. Stebner, D. Maier, A. Ismail, M. Dölz, B. Lohmann, W. Volk, S. Münstermann, “Extension of a Simulation Model of the Freeform Bending Process as Part of a Soft Sensor for a Property Control,” KEM, 926, 2022, doi: 10.4028/p-d17700.
- S. Stebner, D. Maier, A. Ismail, M. Dölz, B. Lohmann, W. Volk, S. Münstermann, “Sensitivity Analysis of Barkhausen Noise Measurements for Residual Stress Correlation,” SMSI 2023, doi: 10.5162/SMSI2023/D1.2. (Accepted)
- A. Ismail, D. Maier, S. Stebner, W. Volk, S. Münstermann, B. Lohmann, “A Structure for the Control of Geometry and Properties of a Freeform Bending Process,” IFAC-PapersOnLine, 54(11), 2021, doi: 10.1016/j.ifacol.2021.10.060.
- A. Ismail, D. Maier, S. Stebner, W. Volk, S. Münstermann, B. Lohmann, “Control System Design for a Semi-Finished Product Considering Over- and Underbending,” Eng Proc, 26(1), 2022, doi: 10.3390/engproc2022026016.
- D. Maier, L. Scandola, M. Werner, S. Stebner, A. Ismail, B. Lohmann, S. Münstermann, W. Volk, P. Lechner, “Experimental analysis on the influence of freeform bending on Barkhausen noise for steel tubes,” in Materials Research Proceedings, 28, 2023, doi:10.21741/9781644902479-224 .
- S. Stebner, D. Maier, A. Ismail, M. Dölz, B. Lohmann, W. Volk, S. Münstermann, “Konzeption eines Softsensor für das Freiformbiegen mit beweglicher Matrize,” in 33. ASK-Umformtechnik.
- A. Ismail, D. Maier, S. Stebner, W. Volk, S. Münstermann, B. Lohmann, “Free-form Bending Control using Optimal Residual Strategies,” IFAC-PapersOnLine, 56(2), 2023, doi: 10.1016/j.ifacol.2023.10.1358.
- S. Stebner, J. Martschin, B. Arian, S. Dietrich, M. Feistle, S. Hütter, R. Lafarge, R. Laue, X. Li, C. Schulte, D. Spies, F. Thein, F. Wendler, M. Wrobel, J. Rozo Vasquez, M. Dölz, S. Münstermann, ”Monitoring the evolution of dimensional accuracy and product properties in property-controlled forming processes”, AIME, 8, 2023, doi: 10.1016/j.aime.2023.100133.