Gesteuerter fest-flüssig Übergang beim Gießwalzen
Bei Umformprozessen wirkt das Werkzeug auf das Werkstück hochgradig nichtlinear, zeitlich und örtlich verteilt. Existierende Regelungsmodelle und Gleichungen können nicht die Schwankungen aufgrund des Umformprozesses berücksichtigen, wie z.B. Legierungszusammensetzung, Umformgeschwindigkeitsschwankungen, Temperatur u.ä.
Als beispielhaften umformtechnischen Prozess wird das Gießwalzen von Magnesiumlegierungen verwendet, bei dem in der Prozesszone vor der Umformung noch ein Urformprozess stattfindet. Das Gießwalzen ist infolge der freien Oberflächen zwischen Düse und Walzen sowie der a-priori unbekannten Lage und Form des Erstarrungsbereiches ein freies Randwertproblem und als Prozess metastabil. Regelungstechnisch und, infolge fehlender belastbarer Messdaten, modelltechnisch ist das Gießwalzen in Verbindung zu den daraus resultierenden Werkstoffeigenschaften nur teilweise verstanden bzw. evaluiert. Messtechnische und modelltechnische Unsicherheiten sind durch das Fehlen von Messdaten insbesondere für die Lage und Form des Erstarrungsbereiches beim Gießwalzen gegeben und sollen im vorliegenden Projekt durch eine neu zu entwickelnde in der Walze integrierte Sensorik beseitigt werden.
Die Mikrostruktur und die finalen Bandeigenschaften können momentan zu keinem Zeitpunkt der Umformung im gesamten Werkstoff erfasst werden. Damit können nicht alle Störungsfaktoren im Modell Berücksichtigung finden. Die Unsicherheiten, die einer robusten, eigenschaftsbasierten Regelung des Gießwalzprozesses im Wege stehen, sollen nunmehr durch quantitative Erfassung von Spannungszustand sowie Temperatur bzw. Wärmestrom im Gießwalzspalt beseitigt werden. Es müssen werkstoff- und messtechnisch robuste Messsysteme und Softsensoren entwickelt werden, die bei dynamischen Messungen zuverlässig den mikrostrukturellen Zustand aus messbaren Größen schätzen lassen. Aus der Zusammenarbeit wird ein grundlegender Erkenntnisgewinn über die Gestaltung resilienter, mikrostruktur- und eigenschaftsgeregelter Umformprozesse erwartet.
Der Gießwalzprozess zur Herstellung von Blechhalbzeugen aus Mg-Legierungen ist mit hohen Temperaturen und vergleichsweise niedrigen Umformkräften in der fest-flüssig Zone verbunden, wobei die verschiedenen Einflussgrößen starke Schwankungen der Mikrostruktur des Bleches hervorrufen. Dabei spielen Position und Verlauf der Erstarrungsfront sowie deren relative Lage zur Fließscheide im durcherstarrten Bereich eine entscheidende Rolle für die Mikrostrukturbildung im Halbzeug.
Die örtlich aufgelöste Messung von Temperatur- und Druckverteilungen auf und in der Walze sollen in Verbindung mit Kennfelder generierenden Simulationsmodellen für den Gießwalzprozess u.a. Informationen über Lage und Form der Erstarrungsfront sowie den Spannungs- und Formänderungszustand liefern und in Verbindung mit angepassten Werkstoffmodellen einen Rückschluss auf den mikrostrukturellen Zustand des Blechs im laufenden Gießwalzprozess ermöglichen.
Durch Erstellung einer Korrelation zwischen Sensordaten an der Walzenoberfläche im Gießspalt sowie zusätzlichen Messstellen außerhalb und den erzeugten finalen Eigenschaften wie Zugfestigkeit, Bruchdehnung, Härteverteilung und Homogenität der Mikrostruktur soll die Voraussetzung eines mikrostruktur- und eigenschaftsgeregelten Gießwalzprozesses geschaffen werden.
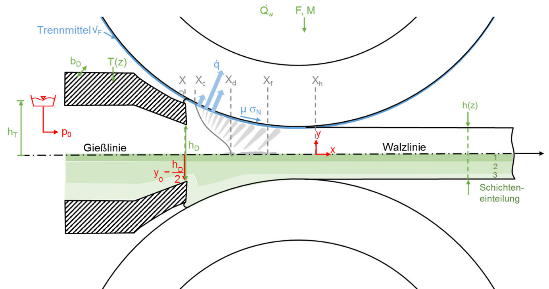
Kontakt
Professur Adaptronik und Funktionsleichtbau der Technischen Universität Chemnitz
Projektleiter: Prof. Dr.-Ing. Welf-Guntram Drossel
Institut für Metallformung der Technischen Universität Bergakademie Freiberg
Projektleiter: Prof. Dr.-Ing. Ulrich Prahl
Dieses Projekt wurde zum Ende der ersten Phase 2021 abgeschlossen.